Faire du ciment
Le ciment entre dans la constitution d’un grand nombre de matériaux : enduits, mortier, béton… Mais quelles sont ses spécificités ? Existe-t-il plusieurs types de ciments ? Comment en fabriquer ? Voici ce que vous devez savoir sur le sujet.
Le ciment, qu’est-ce que c’est ?
Le ciment est une poudre minérale agglomérante qui agit comme liant hydraulique (la poudre durcit très rapidement au contact de l’eau et permet de lier différents matériaux ou agrégats entre eux).
Le ciment joue ainsi le rôle de liant hydraulique dans la composition du béton (lorsqu’on ajoute à la poudre de ciment et à l’eau du sable et des granulats) mais aussi du mortier (sable, ciment, eau) par exemple. Il est également possible d’utiliser le ciment tel quel pour reboucher des trous ou lisser des irrégularités sur une surface donnée (la poudre de ciment doit être mélangée avec juste un peu d’eau).
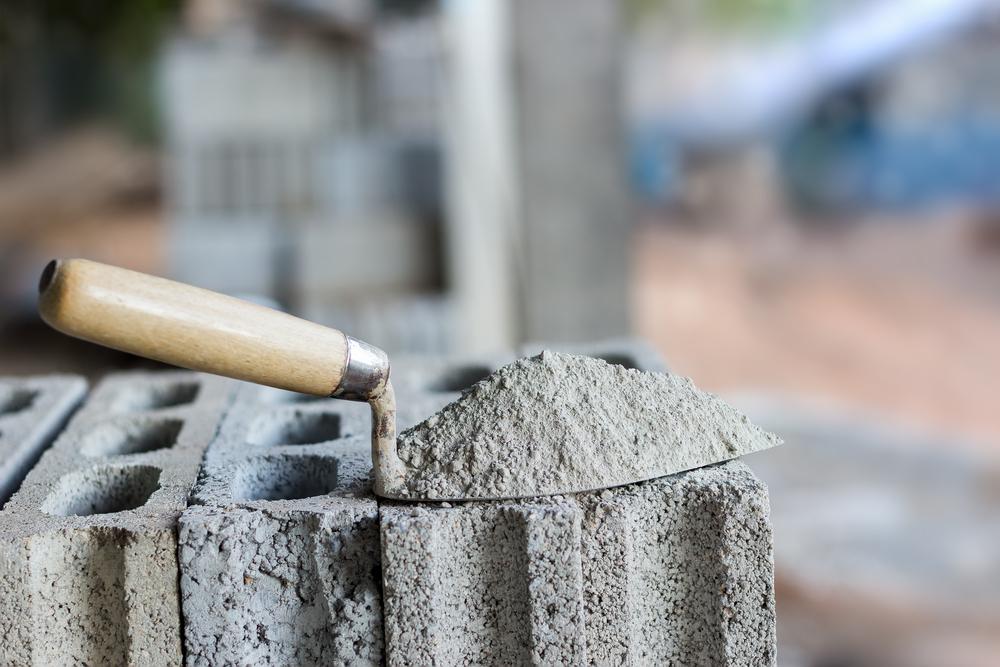
Généralement, la poudre de ciment a une couleur grise, mais elle peut également être blanche ou encore colorée. Le prix sera en revanche plus élevé ! Il faut compter environ 0,25 € / kg pour un sac de ciment classique, contre pas moins de 0,6 € / kg pour du ciment blanc, par exemple. Le conditionnement du ciment quel qu’il soit se fait généralement en sac de 25 ou 35 kg.
Comment faire du ciment ?
Avant toute chose, il faut savoir que le ciment en poudre est fabriqué en cimenterie (ou usine à ciment). Sa fabrication n’est pas à la portée d’un particulier.
Très concrètement, des roches calcaires (silice, chaux…) et de l’argile sont récupérées en carrière puis broyées en éléments de 50 mm maximum. Le mélange broyé (composé à 80% de roches calcaires et à 20% d’argile) est ensuite chauffé à 1 450°C au moyen d’un four rotatif. Cette température élevée permet l’évolution du mélange, qui entre en “zone de clinkérisation”. Une fois sorti du four, le mélange est ensuite refroidi très brutalement. Le matériau granulaire qui en ressort est appelé “Clinker”. Ce matériau est encore une fois broyé. Sa mouture donne finalement la poudre de ciment telle que nous la connaissons.
Le ciment traditionnel dit “Ciment de Portland” est composé au minimum de 95% de Clinker. Mais il existe d’autres types de ciments dont la formulation varie !
Au clinker, on ajoute plus ou moins de constituants dits “secondaires”, qui peuvent être du schiste calciné (T), de la fumée de silice (D, limitée à 10% dans le CEM II), de la cendre volante siliceuse (V), du pouzzolane (P), du calcaire (L ou LL) ou encore des laitiers granulés de hauts fourneaux (S).
Voici les caractéristiques des principaux types de ciments selon leur dosage en clinker :
Ciment CEM I - Ciment de Portland
- Composition :95 à 100% de clinker (noté K)
- Usage :utilisé pour tous types de chantiers de béton mais principalement pour les ouvrages de béton à fort effort de compression et lorsqu’un décoffrage rapide est nécessaire. A noter : il s’agit de la classe de ciment la moins écologique, puisque le Clinker est créé à base de ressources naturelles fossiles et que sa fabrication dégage beaucoup de CO2 (930 kg / tonne produite environ).
Ciment CEM II - Ciment de Portland Composé
- Composition :65 à 94% de clinker
- Usage :utilisé pour les ouvrages classiques, de bétons armés ou non.
Ciment CEM III - Ciment de Haut Fourneau
- Composition :5 à 64% de clinker
- Usage :utilisé pour les travaux souterrains en béton (fondations profondes)notamment. Ce ciment produit de faibles émissions de CO2 car le clinker est remplacé par d’autres constituants et le ciment a une faible teneur en sulfates.
Le saviez-vous ?
Les adjuvants à la poudre de ciment
Il est possible d’ajouter à cette poudre des adjuvants spécifiques pour permettre au ciment d’acquérir des propriétés supplémentaires. Celui-ci peut par exemple être résistant à l’eau ou encore aux fortes chaleurs si on intègre de l’oxyde d’aluminium à sa composition. Les propriétés de ces ciments spécifiques sont annotées sur le sac de poudre. Observez attentivement !
Quelles sont les autres caractéristiques du ciment ?
Comme on l’a vu précédemment, chaque ciment est différent ! C’est d’autant plus vrai que chacun se distingue par sa classe de résistance à la compression mais aussi par sa résistance dite “à court terme”. Passons en revue ces différentes caractéristiques.
Caractéristiques du ciment | Détails |
---|---|
Résistance à la compression | Le ciment est particulièrement résistant à la compression, et donne cette caractéristique au béton. Il acquiert toutes ses capacités mécaniques 28 jours après sa pose. La norme NF EN 197-1 définit pour chaque ciment un seuil minimal de résistance à la compression, qui peut être de 32,5, 42,5 ou 52,5 MPa (mégapascal). La classe 42,5 est généralement préconisée pour des ouvrages dont le béton nécessite une classe de résistance supérieure à C25/30 (ou classe de résistance du béton traditionnel), ce qui correspond à une résistance de plus de 30 N/mm² (Newton). Au sein de chacune de ces trois classes, le ciment est ensuite catégorisé selon sa résistance “à court terme”. |
Résistance à court terme | La résistance à court terme constitue la résistance atteinte par le ciment après 2 ou 7 jours de durcissement. Celle-ci peut être : L (faible résistance), N (résistance normale) ou R (grande résistance). Ainsi, un ciment de résistance à la compression 42,5 peut être “42,5 L”, “42,5 N” ou “42,5 R”. En pratique néanmoins, la résistance L n’est pas utilisée. Un ciment de résistance à court terme R quant à lui est utilisé lorsqu’une prise rapide est nécessaire. |
Fabrication et dosage du ciment selon ses besoins
La pâte de ciment s’obtient par mélange avec de l’eau, selon les indications décrites sur votre sac de poudre minérale. Placez votre ciment en poudre dans une auge à mortier. Ajoutez le sable, puis l’eau. Il vous suffit ensuite de mélanger jusqu’à obtention d’une pâte homogène au moyen d’une truelle.
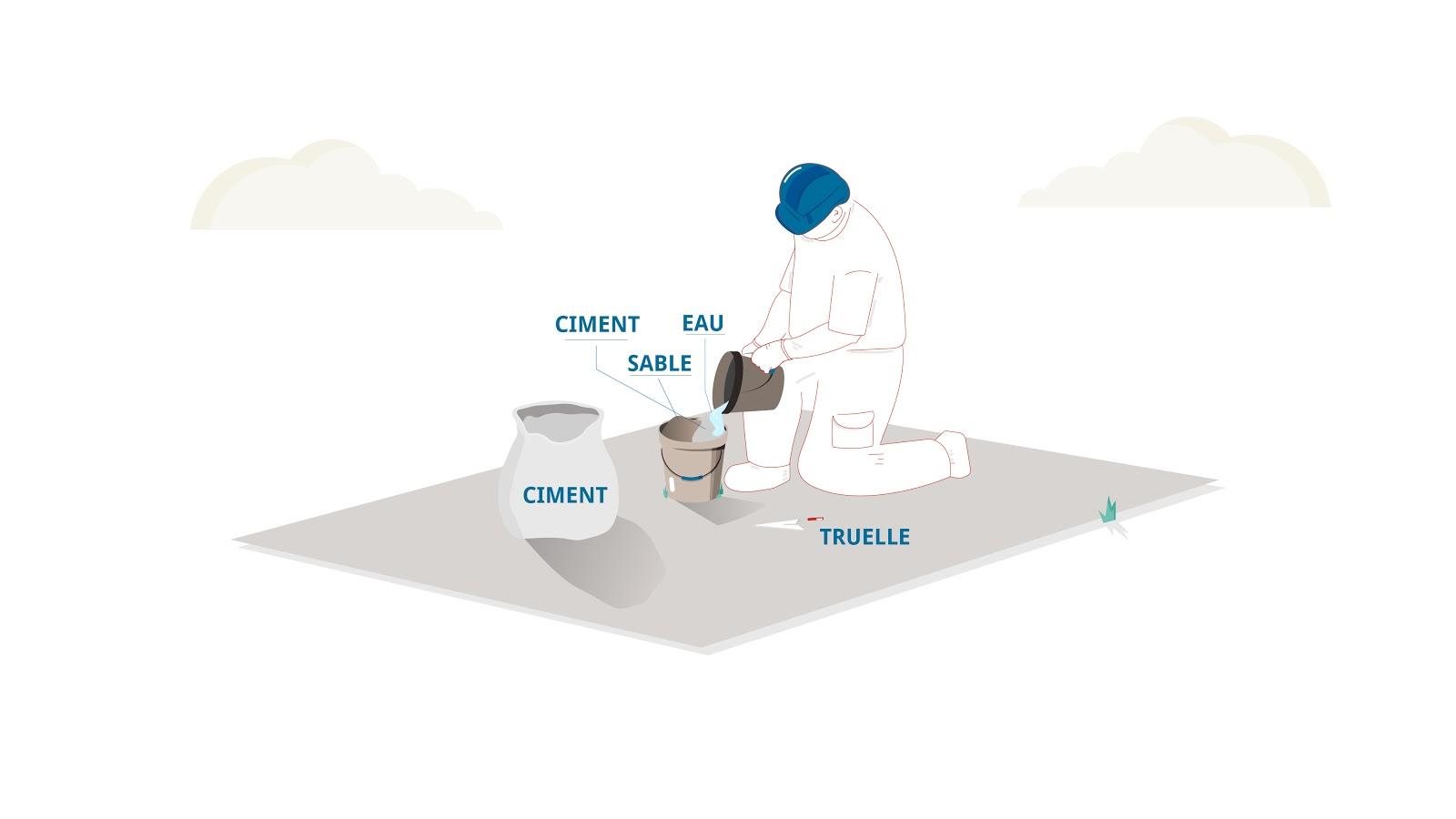
Dans le langage courant, quand on parle de “faire du ciment”, on fait davantage référence à la fabrication de mortier, d’une barbotine ou encore de béton à base de ciment. Quelles proportions de ciment respecter ? Voici quelques informations à ce sujet.
Pour une :
- Utilisation comme enduit de rebouchage : utilisez 3 volumes de ciment pour un volume d’eau
- Fabrication d’une barbotine : mélangez 1 volume de ciment avec ½ volume d’eau
- Fabrication de mortier : ajoutez 1 volume de ciment puis ⅓ d’eau et 3 volumes de sable
Le béton traditionnel quant à lui est dosé à 300 ou 350 kg de ciment / m3. Mélangez 1 volume de ciment avec 2 de sable, 3 de graviers concassés et ½ volume d’eau. Le tour est joué !
Vous l’avez compris : la fabrication du ciment en cimenterie est un procédé lourd et rigoureux. La poudre ainsi obtenue doit ensuite être mélangée avec de l’eau en proportions plus ou moins élevée, selon votre besoin. Fiez-vous aux indications ci-dessus pour vos prochains ouvrages !
Amandine est ingénieur de l'Ecole Centrale de Nantes. Elle est à l'origine de la plateforme de commercialisation de béton au particulier allobeton.com